Philips Dynalite brings its PCB assembly back onshore
Published
2 August 2024
Leader in lighting control, Philips Dynalite, is proud to announce the expansion of its Australian manufacturing facility to include a new state-of-the-art automated Printed Circuit Board Assembly (PCBA) line supplied by Hawker Richardson.
As of July 2024, Philips Dynalite is ramping up local PCBA production, with plans to fully insource this function by the year end.
The new PCBA line will provide end-to-end manufacturing process coverage, from individual electronic components to a finally programmed, tested and packaged product, ready to ship directly to customers worldwide.
In-house PCB assembly will have many benefits for the organisation and its customers, including greater agility when responding to product customisation requests, shorter product lead times, improved stock utilisation, and reduced carbon footprint.
Responsive to customer needs
Many products within the Philips Dynalite portfolio share common components, and onshoring PCB production means the manufacturing team will stock parts for these products at the component level, rather than as work in progress sub-assembly.
Manufacturing Manager, Mark Edwards, explains how this will benefit Dynalite’s customers:
“Setting our own batch sizes off the PCBA line allows us to better balance our resources and enables a smoother workflow within the factory. This means we are not tying up in-demand parts for slower moving assemblies, which will improve our ability to respond to fluctuations in demand with shorter lead times.”
General Manager and Executive Director, Ratko Milosavljevic, explains why autonomous PCB production is critical in a post-COVID-19 world:
“The pandemic presented new business risks with disrupted supply chains and a shortage of common electrical components,” he said. “Onshoring gives us greater control of our destiny, making the business more resilient to external factors and improving our raw material stock utilisation.”
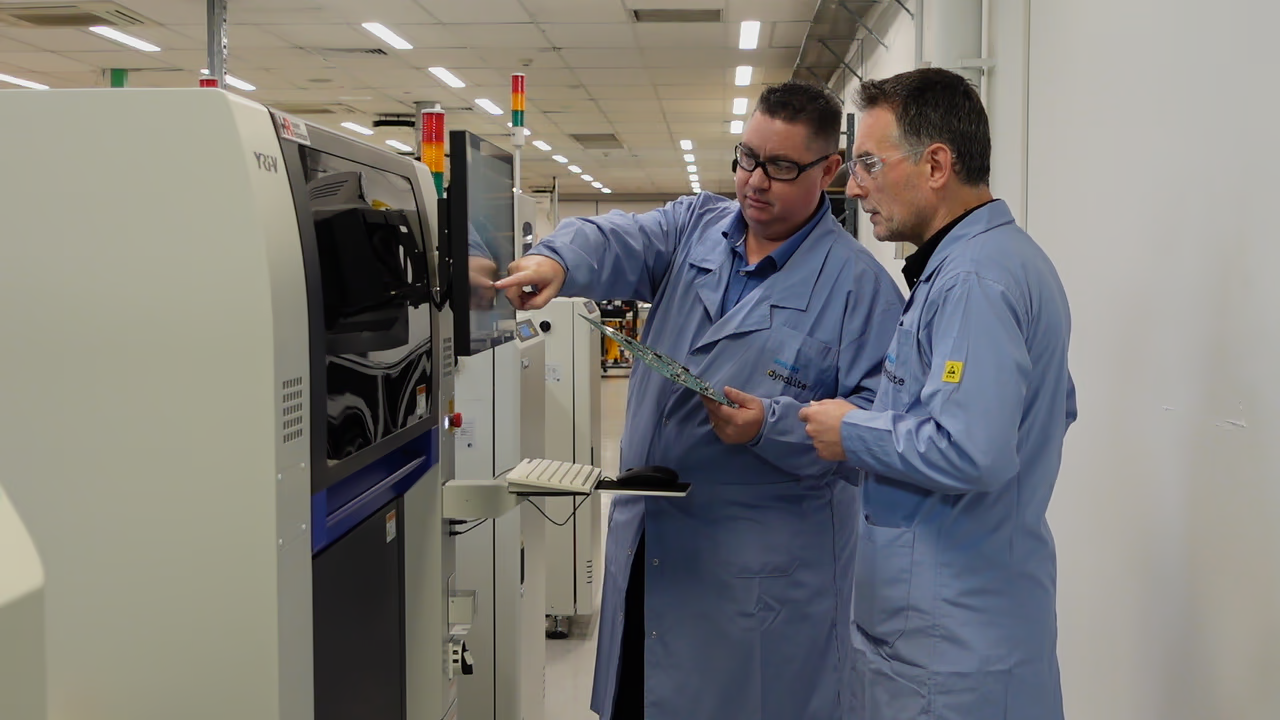
Improved quality and control
Dynalite’s new PCBA line brings significant efficiency and productivity improvements through automation, data exchange, and real-time analytics.
Ratko shares how Dynalite’s quality track record will be maintained through the addition of the new PCBA line:
“The new PCBA line is equipped with predictive maintenance and quality control features, which will support the efficiency of our production line by reducing machine downtime, improving resource utilisation, and reducing waste,” he said.
Hawker Richardson is a well-respected leader in their field with extensive industry knowledge of new equipment and methods in the production of PCBs.
“Our partnership with them for the expansion of our manufacturing facility was an easy choice,” Mark said.
“Modern technological advancements have brought the size of many electrical components down to a fraction of a millimetre, requiring advanced technology in place for total quality control assurance. Philips Dynalite’s new PCBA line includes a state-of-the-art Automated Optical Inspection (AOI) system to deliver quality control with 100% coverage, which traditional quality inspection methods were unable to achieve,” he continued.
Supporting sustainable outcomes
In line with its parent company, Signify, Philips Dynalite has a strong commitment to sustainability across all stages of its supply chain as well as in the on-site performance of its finished lighting control systems.
Procuring raw materials for PCB production will result in less packaging waste, lower transport costs, and reduced carbon footprint compared to importing pre-assembled PCBs.
Ratko expanded on this point, “Lower operational costs will improve our market competitiveness and enable us to pass savings back to our customers. Further, with a smart machine selections such as the HELLER MK7 REFLOW OVEN, we’ve been able to reduce the power usage and carbon footprint of our operations.”
Mark shares how the implementation of this new line aligns with Industry 4.0 standards.
“These technologies move us towards industry 4.0 through the use of AI (for example, by enabling machine learning for predictive maintenance), automation, and new opportunities to enhance sustainable practices. We’ve leveraged Industry 4.0 initiatives to positively impact our productivity, sustainability, and ultimately the community of people around our brand.”
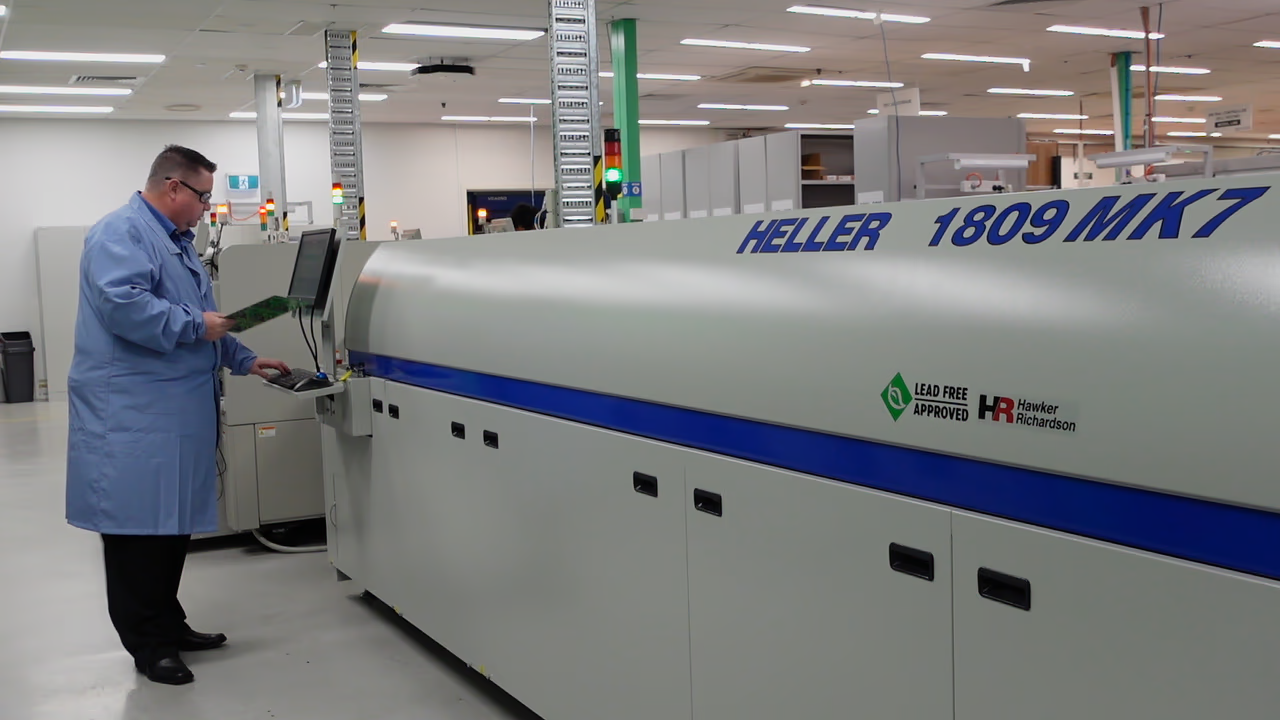
About Philips Dynalite
Philips Dynalite proudly designs and manufactures lighting control equipment in Australia – with a steadfast commitment to the well-being of its people, customers, community, and the planet.
Innovation lies at the core of Philips Dynalite’s offering. The company is dedicated to delivering a robust range of lighting control systems that penetrate to the heart of its customers’ needs – lighting control that is scalable, sustainable, reliable, and human-centric.
The diverse range of lighting control components developed by Philips Dynalite provides installers with all the building blocks they need to create bespoke solutions fit for any application.